The old courthouse stood tall, weathered by time or stories. Tasked with restoring the space, the architect arrived on-site expecting precise as-built documentation. But what they received instead was an outdated 2D drawing with mismatched dimensions. Weeks were lost, costs ballooned, and frustration mounted until a new point cloud survey and a Scan to BIM model brought the project back on track. This isn’t just one firm’s story; it’s a common scenario across the AEC industry. With the rise in renovation and infrastructure modernization, Scan to BIM services in USA are becoming indispensable for capturing existing conditions with millimeter precision. By converting laser scans or photogrammetry into detailed 3D models, point cloud to BIM ensures teams work with reliable, data-rich visuals.
The technology is no doubt powerful, but even the most advanced point cloud to BIM modeling services can fall short if the project scope is unclear, the scan data is flawed, or workflows are poorly managed.
In this article, we’ll highlight Five common mistakes in Scan to BIM projects and how to avoid them. Whether you're an architect, engineer, or surveyor, you’ll gain insights to help you reduce rework, improve coordination, and ensure smoother project delivery every time.
5 Common Mistakes in Scan to BIM Projects And How to Fix Them
While Scan to BIM offers greater benefits from improved accuracy to streamlined renovations, many projects stumble due to avoidable errors. Recognizing these pitfalls early can save time, reduce costs, and ensure a seamless workflow.
Below are five common mistakes teams make while providing Point cloud to BIM Modeling Services, along with practical strategies to prevent them.
Incomplete or Low-Quality Point Cloud Data
One of the most common issues in Scan to BIM projects starts at the very beginning, with the scan itself. When scan data is incomplete, noisy, or captured at a low resolution, the resulting point cloud lacks the clarity needed for accurate modeling. This often happens due to subpar equipment, poor lighting, obstructed views, or incorrect scanner settings.
The impact?Gaps in geometry, missing elements, and unreliable references that slow down the modeling process, lead to multiple rounds of rework, and delay project delivery.
How to Avoid This:- Use high-quality laser scanners with the right resolution and range for your project type.
- Ensure sufficient scan overlap and proper registration to stitch all scans seamlessly.
- Always validate your point cloud data for completeness and accuracy before modeling begins.
- Partner with experienced survey teams or trusted Scan to BIM service providers who understand site conditions and scanner limitations.
Whether you're delivering architectural as-builts modeling or detailed MEPF layouts, the foundation of any successful point cloud to BIM workflow lies in clean, reliable scan data. Getting this right is the first step toward delivering accurate, efficient, and scalable point clouds to 3D modeling services.
Insufficient Pre-Scan Planning
The most advanced scanners can’t save a project if the groundwork isn’t done right. One of the costliest oversights in Scan to BIM services is jumping into scanning without a clear plan. Failing to define scan locations, angles, or the required Level of Detail (LOD) often results in missed critical elements, like overhead MEP systems, structural connections, or tight mechanical rooms.
The impact?Incomplete point cloud, fragmented models, and site revisits that inflate both time and cost.
How to Avoid This:- Begin with a thorough pre-scan site assessment. Walk the site to identify access limitations, reflective surfaces, or areas that may require special attention.
- Clearly define the LOD expectations and modeling scope in advance, what you need to capture, and to what level of precision.
- Plan optimal scan positions and overlaps using scan planning software to reduce blind spots and improve efficiency.
Whether you're delivering point cloud to BIM modeling process for architecture, MEP, or facility management, proper planning ensures you collect the right data the first time, saving hours in the field and weeks in production.
Overlooking Data Cleaning & Filtering
Point clouds don’t come perfectly straight out of the scanner. Raw scan data often includes noise, people moving through the space, construction debris, equipment, or environmental interference. Yet many teams make the mistake of importing this unfiltered data directly into modeling software, expecting smooth results.
The impact?Cluttered models, increased processing times, and higher chances of errors in geometry and alignment, especially when delivering precise point cloud to BIM modeling services.
How to Avoid This:- Use tools like Autodesk ReCap, CloudCompare, or Faro Scene to clean and filter your point cloud before modeling. These platforms allow you to remove irrelevant data, reduce file size, and improve clarity.
- Segment the point cloud to isolate only the relevant building elements, such as walls, beams, MEP systems, and structural components, based on your LOD requirements.
- Always perform a QA check after filtering to ensure no critical data has been removed.
In high-stakes projects across the USA, professional Scan to BIM services prioritize data cleaning as a non-negotiable step. Clean inputs mean faster turnaround, fewer errors, and more accurate point cloud to BIM deliverables.
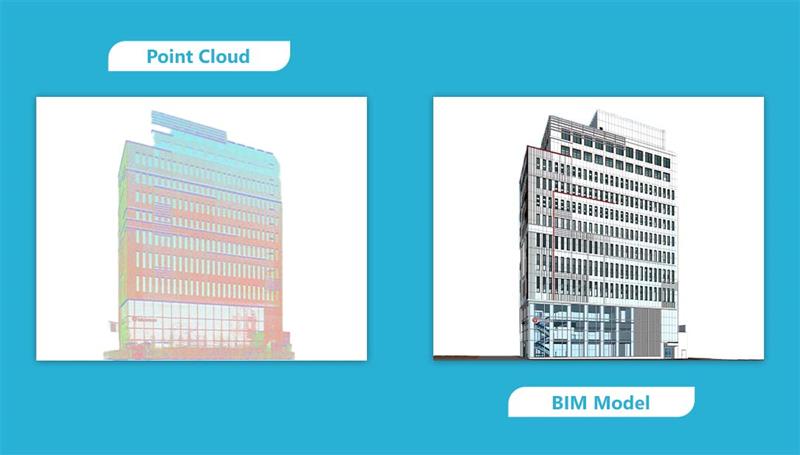
- Location : USA
- Type of Building : Residential
- Level of Detail (LOD) : 300
- Trades Covered : Architecture, Structure & MEPF Model
- Software : Revit
Undefined Level of Detail (LOD) and Level of Accuracy (LOA)
One of the biggest challenges in point cloud to BIM workflows is misalignment between what the client expects and what the modeler delivers. Without a clear definition of Level of Detail (LOD) and Level of Accuracy (LOA), teams risk either remodeling, which wastes time and budget, or undermodeling, which fails to meet project requirements.
The impact?Disputes over deliverables, costly rework, and delays in downstream processes like coordination, fabrication, or facility management.
How to Avoid This:- Define LOD and LOA upfront: For example, use LOD 300 for design coordination or LOD 500 for facilities management, depending on project needs. Adopt LOA standards from USIBD or project-specific guidelines to ensure consistency in measurement accuracy.
- Develop and maintain a BIM Execution Plan (BEP): that documents scope, deliverables, model use cases, and quality benchmarks. This becomes the single source of truth for both client and production teams.
Leading Best Scan to BIM services providers in the USA rely on this level of clarity to ensure their point cloud to BIM modeling services are aligned, scalable, and purpose-built, right from the first file.
Ignoring Tolerances and Real-World Deviation
In a digital world, it’s tempting to model everything as perfectly straight, level, and aligned. But in the real world, buildings shift, sag, and settle. Ignoring these real-world deviations and modeling to “ideal” geometry can lead to serious issues during construction or renovation.
The impact?Clashes, misalignments, and costly change orders, especially when prefabricated elements don’t fit on-site.
How to Avoid This:- Always model within tolerances that reflect actual field conditions. Instead of forcing geometry into perfect lines, allow for natural imperfections captured in the point cloud.
- Use deviation analysis tools like Navisworks or Verity to compare modeled geometry against the original scan data. These tools help highlight areas where adjustments are needed to match as-built reality.
- Clearly communicate allowable tolerances in your Scan to BIM workflow and documentation.
By acknowledging the imperfections captured in the point cloud to BIM process, teams can create models that are not only accurate but also constructible. That’s what separates generic models from true point cloud to BIM modeling services that deliver real value on-site.
Conclusion
As the AEC industry increasingly relies on Scan to BIM to bridge the gap between existing conditions and digital design, the importance of precision, clear communication, and standardized processes cannot be overstated. From capturing high-quality point cloud data to defining LOD and validating real-world deviations, every step plays a critical role in delivering accurate and dependable models. By avoiding the common mistakes discussed, like poor scan planning, unfiltered data, and undefined modeling scopes, teams can significantly improve accuracy, reduce rework, and save both time and money. More importantly, they can boost trust and collaboration across all stakeholders.
However, a successful point cloud to BIM project isn’t just about producing a visually clean model; it’s about creating a reliable digital twin that supports real-world construction and operations. And that requires more than good software; it demands good processes.
Whether you're offering or outsourcing point cloud to BIM modeling services, investing in the right training, tools, and pre-project planning is essential. It ensures your team is aligned, your deliverables are consistent, and your outcomes are measurable.
If you’re looking for accurate, clash-free, and data-driven BIM models from your scan data, trust the experts at scantoBIM.online to get it right the first time.